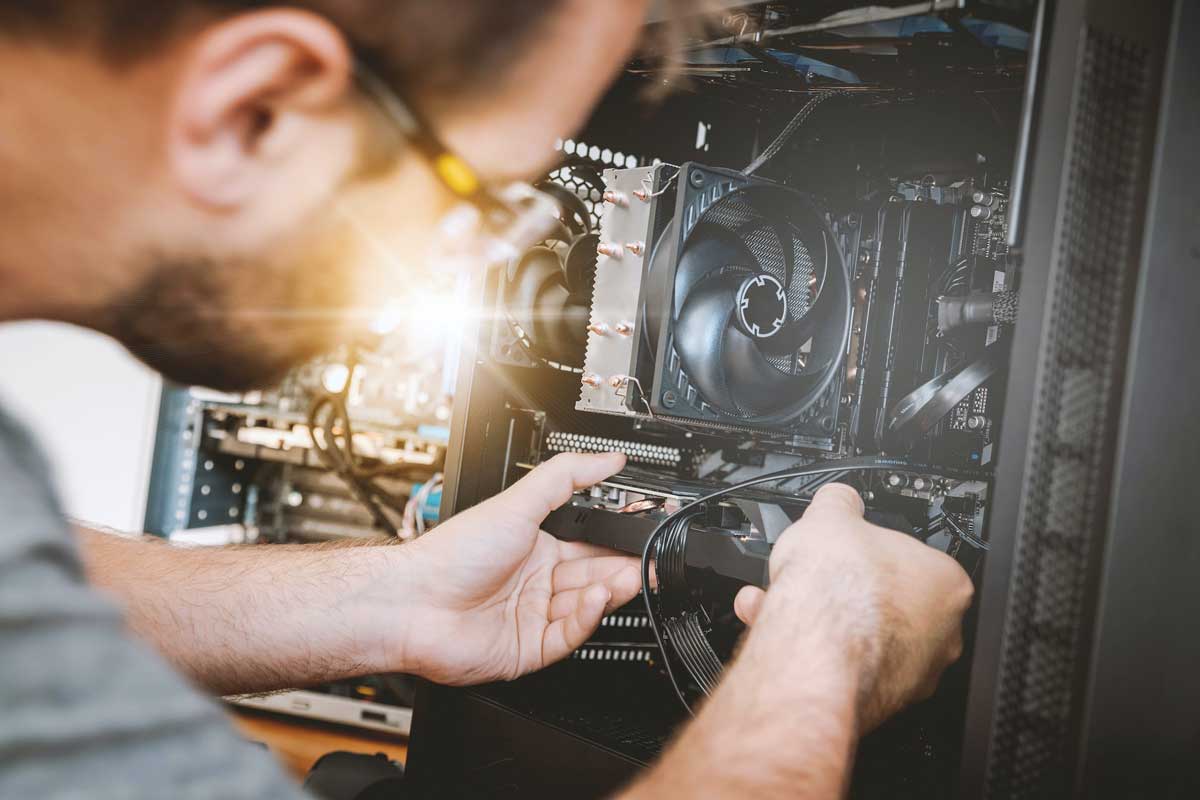
Harnessing the Power of Proactive Maintenance in IT for Effective Equipment Replacement Planning
In the dynamic world of Information Technology (IT), asset longevity and optimal performance are paramount. To keep your systems running smoothly, it's crucial to understand and implement proactive maintenance strategies. The crux of these strategies often lies in judicious equipment replacement planning based on critical factors such as end-of-life (EOL), equipment age, workload, and others. This guide will walk you through the essence of proactive maintenance and elucidate the methods for effective equipment replacement planning.
Understanding Proactive Maintenance in IT
Proactive maintenance refers to a preemptive approach that focuses on preventing equipment failures before they occur, rather than simply reacting to them. This strategy offers an array of benefits: improving system performance, extending the life of IT assets, reducing repair costs, and minimizing unexpected downtime.
By implementing a proactive maintenance regime, organizations can detect potential issues early, allowing ample time for resolution and helping maintain operational continuity. This system anticipates equipment faults and defects, often through regular monitoring, predictive analytics, and trend tracking.
Equipment Replacement Planning: Why It Matters
Equipment replacement planning is an integral component of proactive maintenance in IT. This involves determining the optimal time to replace equipment to prevent failures, minimize costs, and maximize performance.
Effective replacement planning balances the cost of keeping old equipment running—through increased energy usage, more frequent repairs, and lower efficiency—with the cost of acquiring and integrating new equipment.
Factors Influencing Equipment Replacement Decisions
A myriad of factors can guide equipment replacement decisions in IT. Here are the most significant ones:
End-of-Life (EOL)
The EOL of a device is the date beyond which the manufacturer no longer supports the product with updates, patches, or customer support. EOL is often a clear indication that the equipment needs replacement to ensure system security and performance.
Equipment Age
Age is a primary consideration. Older equipment tends to fail more frequently, operates less efficiently, and often lacks the capabilities of more modern technology. However, age alone should not dictate replacement. Some devices might continue to perform efficiently well past their expected lifespan, depending on their use and maintenance.
Workload
The level of use or workload an equipment endures can significantly impact its lifespan. Devices running at high capacity continuously are likely to wear out faster than those under lighter workloads.
Technological Advancements
Technology advances rapidly, and newer devices often provide better performance, energy efficiency, and features. Even if the old equipment is still functional, the benefits of upgrading might outweigh the costs.
Maintenance and Repair Costs
As equipment ages and undergoes more extensive use, maintenance and repair costs increase. When these costs approach or exceed the cost of replacement, it is often more economical to replace the equipment.
The Role of Predictive Analytics in Proactive Maintenance
Predictive analytics, driven by AI and machine learning, play an essential role in proactive maintenance. These technologies analyze historical data to identify trends and patterns, predict potential failures, and provide actionable insights for effective equipment replacement planning.
Conclusion
Proactive maintenance in IT is more than just a preventive measure—it's a strategic approach to maintain optimal performance, prevent unnecessary downtime, and achieve cost-efficiency. Implementing effective equipment replacement planning, factored by elements
Ready to Optimize Your IT Infrastructure?
Don't let outdated equipment and unplanned downtime hinder your business growth. At ALL I.T. LLC, we specialize in proactive maintenance and strategic equipment replacement planning. Our expert team uses advanced predictive analytics to help you make informed decisions that extend the life of your IT assets, optimize performance, and maximize your return on investment.
Get ahead of potential issues and ensure your IT infrastructure is running at peak efficiency. Contact ALL I.T. LLC today for a comprehensive consultation on proactive maintenance and equipment replacement planning. Let's build your future-proof IT strategy together.
IT equipment can fail due to various reasons, often relating to a combination of hardware, software, and environmental factors. Here are some of the most common reasons:
- Overheating: Overheating can damage internal components, leading to equipment failure. This typically occurs when devices are not adequately ventilated or operated in high-temperature environments.
- Power Issues: Power surges, outages, and brownouts can damage electrical components, causing equipment failure. Uninterrupted Power Supply (UPS) systems and surge protectors can help prevent such incidents.
- Hardware Failure: Hardware components, like hard drives, power supplies, or memory modules, can physically fail, especially with age and continuous use.
- Software Errors: Software bugs, corruption, and incompatibilities can cause system crashes and equipment failure.
- Dust and Dirt: Dust can accumulate on internal components, leading to overheating and, eventually, failure. Regular cleaning can help avoid such issues.
- User Errors: Accidental deletion of critical system files, mishandling of hardware, or incorrect system modifications can lead to equipment failure.
- Lack of Maintenance: Failure to regularly update software, replace aging components, or perform preventive maintenance can lead to system instability and equipment failure.
- Manufacturer Defects: Faults in the manufacturing process or design of IT equipment can cause failure.
- Cyber Attacks: Malware or cyber attacks can cause system crashes, data corruption, and hardware failure in severe cases.
- Electrostatic Discharge (ESD): Electrostatic discharge, while installing or handling components, can cause instantaneous damage or gradual component degradation, leading to failure over time.
Remember, regular proactive maintenance and monitoring can help identify and rectify many of these issues before they result in equipment failure and significant downtime.
Are the above common IT equipment failures covered by insurance companies?
Insurance coverage for IT equipment failures can vary significantly based on the specific insurance policy and the company providing it. In general, some common IT equipment failures may be covered by certain insurance policies, but it's essential to thoroughly understand the terms and conditions of the specific policy.
Commercial Property Insurance generally covers the physical loss or damage to the property (including IT equipment) due to covered causes such as fire, theft, or natural disasters.
Equipment Breakdown Insurance (sometimes called "boiler and machinery" insurance) typically covers the cost to repair or replace equipment that breaks down due to power surges, motor burnout, operator error, and similar incidents. It may also cover business interruption losses resulting from the equipment breakdown.
Cyber Insurance can cover losses related to cyber attacks or data breaches. This could include costs related to data restoration, legal fees, or business interruption due to a cyber event.
However, it's important to note that insurance typically does not cover failures due to normal wear and tear or lack of maintenance. Additionally, certain perils such as flooding may require separate coverage. Always review your policy details or consult with an insurance professional to understand what is covered and any policy exclusions or limitations.
Keep in mind that insurance should not be seen as a substitute for proactive IT maintenance and robust cybersecurity measures. Maintaining your IT equipment properly and securing it from cyber threats can help prevent many issues from arising in the first place.
If the above equipment were to fail from lack of Proactive Maintenance, what are the costs to most SMB to recover from these failures?
The cost to recover from IT equipment failure due to a lack of proactive maintenance can vary significantly based on several factors, including the type and extent of the failure, the size of the business, the specific equipment involved, and the business sector. However, below are a few common costs that many small to medium-sized businesses (SMBs) may face in such situations:
- Hardware and Software Replacement Costs: When IT equipment fails, it often needs to be replaced or upgraded. The cost of new hardware or software can be substantial, especially for specialized or high-end equipment.
- Data Recovery Costs: If data is lost due to equipment failure, professional data recovery services may be needed, which can be expensive. Furthermore, not all lost data can be recovered, leading to potential irretrievable loss.
- Downtime Costs: When IT equipment fails, the downtime can lead to significant losses. This can include lost sales, reduced productivity, and potential reputational damage if the downtime impacts customers or clients.
- Repair Costs: If the equipment can be repaired, there will still be costs associated with parts and labor. In some cases, expedited repair services may be needed, which can be more expensive.
- Incident Response and Forensics: In the event of a cybersecurity incident resulting from failed equipment, incident response and forensic analysis can be a significant cost.
- Regulatory Fines and Legal Costs: For businesses that handle sensitive information, equipment failure that leads to a data breach can result in regulatory fines and potential lawsuits.
- Increased Insurance Premiums: Businesses that experience frequent equipment failures might face higher insurance premiums.
It's important to remember that these are potential costs and that the actual cost for a specific business will depend on various factors. However, investing in proactive maintenance can help prevent many of these costs by identifying potential issues early and allowing them to be addressed before they lead to equipment failure. Investing in proactive maintenance can also extend the life of IT equipment, leading to lower total cost of ownership over time.
How often is does the labor and parts repair cost out weigh the complete replacement of the hardware weighing the age factor and parts availability?
The decision to repair or replace a piece of IT equipment is a common dilemma. Several factors influence this decision, including the cost of repair, the age of the equipment, the availability of replacement parts, and the potential benefits of using newer technology.
Repair costs can quickly add up, especially for older equipment. Labor rates for skilled IT professionals are substantial, and the cost of parts, particularly for older or rare models, can be high. If a piece of equipment is old, it might break down again soon, even after being repaired, leading to more costs down the line.
As a general rule of thumb, if the cost of repairing a piece of equipment is more than 50% of the cost of a new equivalent, it's often more economical to replace it. This rule isn't absolute, though, and other factors should be taken into consideration.
Age is a significant factor. Older equipment is typically more prone to failures, less efficient, less compatible with new technology, and more costly to maintain. Parts for older equipment can also be harder to find, and their installation may require specialized knowledge.
When evaluating repair versus replacement, it's also important to consider indirect costs such as potential downtime, lost productivity, and the impact of using outdated technology. New equipment often provides benefits such as improved performance, energy efficiency, and features that can lead to increased productivity and other cost savings.
In the fast-paced world of IT, maintaining and repairing outdated hardware can sometimes feel like a losing battle. Proactive maintenance and regular equipment upgrades can prevent many issues and costs associated with equipment failures and can lead to a more reliable and efficient IT infrastructure.
Ignite Your Business Potential with Proactive IT Maintenance and Managed IT Services
Don't let IT equipment failure and unexpected downtime slow your business momentum. ALL I.T. LLC specializes in Proactive IT Maintenance and Managed IT Services designed to keep your systems running at their peak, minimize downtime, and ensure you're always ahead of the curve.
With our Proactive IT Maintenance program, you can rest assured that your IT infrastructure is in expert hands. We take a preventative approach to mitigate risks before they evolve into costly repairs or replacements. We understand that every minute counts in today's fast-paced business environment, and our goal is to ensure your operations run smoothly and efficiently.
In addition, our Managed IT Services free up your resources to focus on core business functions. Leave the intricacies of IT to us. From network management and data protection to cloud services and IT consulting, we've got you covered.
Don't wait for a crisis to take action. Invest in your business's future and resilience today. Reach out to ALL I.T. LLC at 231-375-8682 to discuss how our Proactive IT Maintenance program and Managed IT Services can streamline your operations, enhance your performance, and optimize your IT investments. We're here to empower your success.